|
|
|
High-power Fibers for
Diode Lasers |
|
|
High Power (HP-) Silica Cables are assembled with
innovative HP-SMA-connectors made with inner Copper ferrules for free
fiber end position and capable for durable delivery of laser power of
high intensity in pulsed or cw mode in the range below 1kW (cw).
Super High Power (SHP-) Silica Cables could deliver up to
several kW from Diode and Solid State lasers resulting from their
assembly with a larger size SHP-connectors of special design with
diameter spans 2.5, 4, 10 and 15mm - or with Mitsubishi connectors of
D-80 and D-200 types. Bespoken SHP-connector design may include Copper
ferrule protection by Sapphire rings to prevent Copper evaporation by
intensive laser beam.
Fiber Core
Diameter (μm) |
100
|
200
|
400
|
600
|
800-1000
|
1000-2000
|
Max Power
(kW) |
>0.1
|
>0.6
|
>1
|
2-4
|
6-8
|
>8
|
HP- and SHP-cables
can be protected by polymer coated metal armor or MKS-jacketing
(Stainless Steel / Kevlar / Silicon) for durable protection of silica
fibers inside � which diameter spans from 100μm to 2mm. In-house
technology of precise assembly allows to assembled single HP & SHP-cables
with a length from 50mm to 100m.
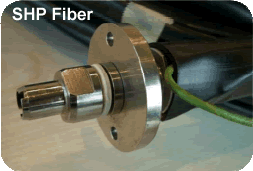
All silica
fiber NA = 0,22, default length 1m, protected in stainless steel
(inside) and fabric silicone (outside) tubing (out diameter 6mm, grey),
terminated with 2x SMA905 free end connectors, electrically disconnected
Part number |
ST-SMA905-F100 |
ST-SMA905-200 |
ST-SMA905-400 |
ST-SMA905-600 |
Fibre core diameter (μm) |
100 |
200 |
400 |
600 |
Fibre cladding diameter (μm)
|
140 |
280 |
480 |
720 |
Max. laser power (W) |
70 |
150 |
150 |
150 |
Short term bending radius (cm)
|
1.1 |
2.1 |
3.6 |
5.4 |
Long term bending radius (cm)
|
4.2 |
8.4 |
14.4 |
21.6 |
1) HP- & SHP-cables based on UV- & NIR-Silica glass for
flexible power delivery of Diode, Solid State, DPSS and Gas lasers �
which durable exploitation is secured by low optical losses in fiber of
special structure, by innovative design of HP- & SHP-connectors, by
proper fiber protection with armored MKS-jackets and by inhouse test of
all cables performance;
2) HP- & SHP-cables based on special Silica fiber coated
by Aluminium, Copper or Copper alloys � where unique technology of metal
freezing on lateral fiber surface doubles fiber bending strength,
accelerates dissipation of laser induced heat from the fiber under
delivery of high power and enables cables applications at high
temperatures up to 600�C;
3) HP-Silica Fiber Summarizers for fiber collection of
power from 3 to 7 Diode Laser Modules - provides above 100W of combined
laser power at the input of HP-Refocusator of special design and then
this refocused power is homogenized by HP-fiber Homogenizer. This 3
component HP-Silica Fiber System provides flexible solution for
multiwavelength laser combination and for medical applications like hair
epilation in cosmetology;
4) HP-Silica Fiber Dental Applicators (SFDA) � for
disposable applications in advanced laser dentistry and ENT laser
surgery. Variety of HP-Silica cables for medical lasers includes the
design where fibers are assembled with electric wires in the same
protective jacket � as it is required for remote control and variation
of laser parameters during laser surgery. Distal fiber ends may be
terminated with a variety of hand-pieces of bespoke design. |
|
Chalcogenide IR-Glass Fiber (CIR Fiber) |
|
Chalcogenide Infra Red (CIR) glasses are the best As2S3-based
material for fiber optics in the range of 1.5-6μm. CIR fibers transmit
IR-radiation in the gap between silica fibers (0.2-2.4μm) and
Polycrystalline Infra Red (PIR) fibers (4-18μm). CIR fiber is drawn in
core/clad structure with double polymer coating and characterized by a
low optical losses and high flexibility.
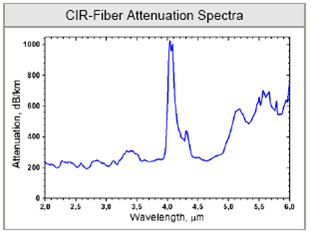
The innovative glass purification process provides the
attenuation spectra free from OH absorption band at 3μm and thus it
enables CIR fiber to be used for Er:YAG laser power delivery.
Features
� high transmittance from 1.5μm up to 6μm
� suitable for Er:YAG - laser power delivery
� optical losses 0.2 dB/m at 2-4μm
� double polymer coating for high flexibility
� durable cables with SMA-connectors
Applications
� Flexible delivery for Er:YAG - laser
� flexible IR-imaging systems
� remote non-contact pyrometry in the 200-600K range
� fiber probes for remote process IR - spectroscopy
Fiber specification
Transmission Range |
1.5 - 6μm |
Core/Clad Structure |
As2S3/As-S |
Core/Clad Diameter |
200-500/300-600μm |
Core Refractive Index |
2.4 |
Effective NA |
0.28 |
Protective Coating |
Double Polymer Jacket |
Ambient Temperature Range |
270 - 370 K |
CIR Infrared Optical Fiber Standard Cables
Chalcogenide Infra Red (CIR) (1.5 - 6μm) fiber is drawn
in core/clad structure with double polymer coating and characterized by
a low optical losses and high flexibility. Delivery is from stock or
within few weeks ARO. All standard cables include PEEK-polymer
protective jacket and SMA termination. |
|
Polycrystalline Infra Red Fibers (PIR � Fibers) |
|
The development of specialty fibers for the Mid-Infrared
region has resulted in a unique product - Core/Clad Polycrystalline
Infra-Red (PIR-) fibers. The PIR-fibers are non-toxic, very flexible,
transparent across a broad spectral region
4
-18μm and capable of operating over the wide temperature range of 4K up
to 420K. They are manufactured in a core/clad structure of superior
quality from pure AgCl: AgBr solid solution crystals using an innovative
vacuum extrusion method. They possess by no aging effect compared to an
alternative bare core fiber. The range of PIR-fiber cables are available
with a durable PEEK polymer jacket and terminations using either an SMA
- type connector with a Ti or polymer ferrule or special one,
manufactured on customer request. A wide variety of different optical
coupling units can also be designed & fabricated for specialized
customer requirements.
Fiber Features:
� high transmittance from 4μm up to 18μm
� high flexibility and no toxicity
� suitable for CO2 - laser power delivery up to 50W
� low Attenuation at 10.6мm (0.1-0.5 dB/m)
� fiber diameters from 0.3 to 1.0mm
� fiber lengths up to 20m (for 0.5mm diameter)
� no aging effect
Standard Fiber Specification:
Standard Fiber Core/Clad Diameters
Other fiber diameters in 0.3-1.5mm range are also
available (request on special fabrication) |
240/300, 400/500, 630/700, 900/1000μm
|
Transmission range |
4-18μm |
Attenuation at 10.6μm |
0.1-0.5 dB/m |
Refractive index |
2.15 |
Standard Effective NA |
0.25 |
Laser Damage Threshold for CW CO2-laser
|
>12 kW/cm2
|
Melting point |
415�C |
Tensile strength |
>100 MPa |
Minimum Bending Radius (fixed)
|
10x[Fiber Diameter] |
Minimum Elastic Bending Radius
|
100x[Fiber Diameter] |
PIR-fibers are protected by a loose PEEK-jacket (PolyEtherEtherKetone)
to provide stiff, flexible and hermetic protection against mechanical,
photoinduced and chemical damage over a wide temperature range up to
250�C.
Standard Cable termination with a special Ti-ferrule SMA-connector:
� for low power (spectroscopy & radiometry) applications;
� for high laser power delivery - free standing fiber end
;
� standard cable length - 1m & 2m.
PIR-fiber end-surface treatment:
� Cutting low cost, high performance - standard;
� Polishing for special application, including AR-coating
- on request;
� SMART for reduced reflection of high CO2-laser
intensity - on request.
Options
� accessory kits for remote spectroscopy with FTIR, QCL
and TDL-spectrometers;
� pig-tailing of IR-detectors: TE- & LN-cooled MCT, PbSe,
thermopiles, etc.
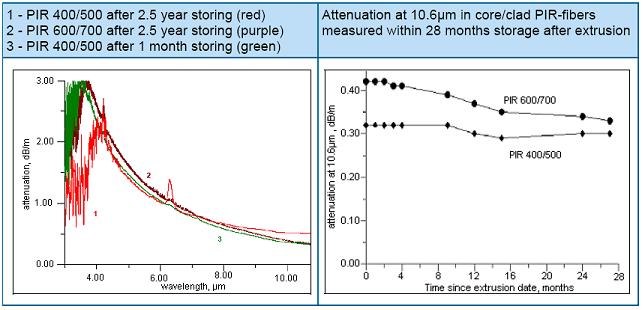
Diverse Methods of AR-coating and SMART-treatment
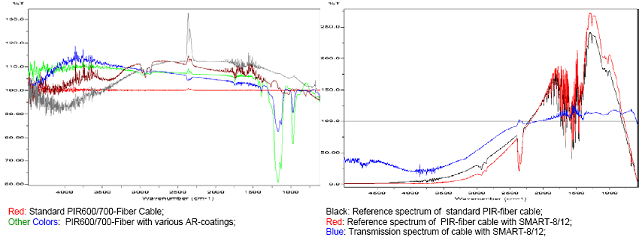
Comparison of Standard and Spectral PIR-fibers
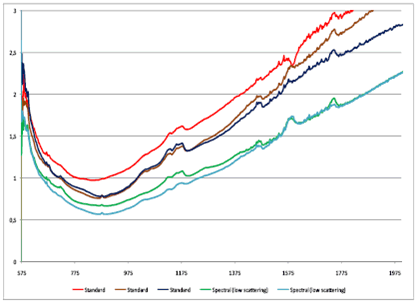
Applications
� Flexible delivery system for CO and CO2 laser;
� Flexible IR-imaging systems;
� Remote non-contact pyrometry in the 100-600K range;
� Fiber probes for remote in-line, in-vivo and process IR
- spectroscopy. |
|
Comparison of CIR- and PIR-Fibers |
|
Typical transmission spectra of 1.5m long PIR-900/1000
fiber (red) versus CIR-750/850 fiber (blue) (includes reflection &
coupling losses at fiber ends without AR coating and some absorption
bands of atmospheric moisture, etc.)
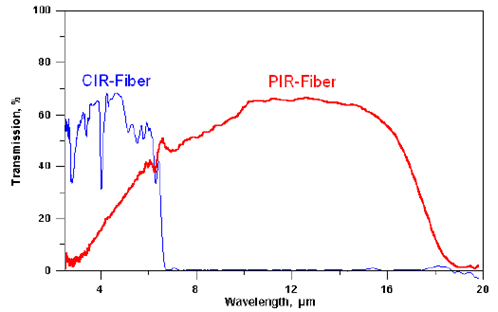
Typical specification of CIR- and PIR-fibers
No. |
Parameter |
CIR-Fiber |
PIR-Fiber |
1 |
Transmission range |
1.5 to 6μm or 1600- 6500cm-1
|
3 to 18μm or 550 - 3300cm-1
|
2. |
Core/Clad structure materials |
Chalcogenide As-S glasses |
AgCl:AgBr solid solution crystals
|
3. |
Specific Features |
Toxic & Fragile, Non-hygroscopic
|
Non-toxic, Non-hygroscopic, very flexible,
slightly UV-sensitive |
4. |
Core/Clad diameter |
200-500/300-600μm |
400/500, 630/700, 700x700, 900/1000μm
|
5. |
Core refractive index |
2,4 |
2,2 |
6. |
Effective NA |
0,28 |
0,25 |
7. |
Optical losses |
Minimum of 0,2dB/m at wavelengths 2-4μm
|
Minimum of 0,2-0,3dB/m at wavelengths 10-12μm
|
8. |
Operation temperature |
From 270 to 370K |
From 4 to 420K |
9. |
Max length of cable |
Up to 50-100 meters |
Up to 20-40 meters |
Comparison of PIR- and CIR-Fibers Transmission Spectra
for 1.5m length
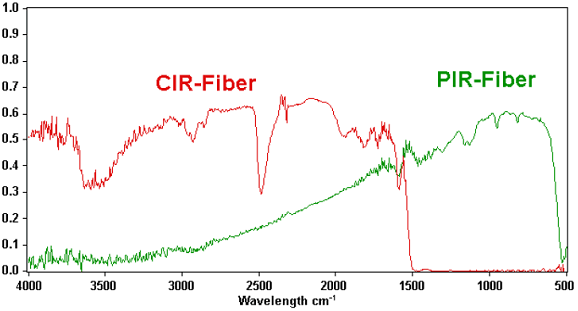
|
High Power Silica Fiber Cables |
We are one
of leading suppliers of high-power silica fiber cables for industrial,
medical and scientific applications. We offer Fiber Cables in a variety
of fiber diameters, protective tubings and connectors, as shown below.
Our High Power Fiber Cables exploit the air-gap-ferrule design, where
the fiber prolongs into free space securing an epoxy-free area where
thermal energy can be safely dissipated without burning the surrounding
material, making them ideal for high-power applications. The connector
ferrules, fabricated from stainless steel and copper, are used as a heat
sink, pulling the heat quickly away from the fiber.
Applications:
■
Laser Welding
■
Laser Cutting
■
Medical Laser Delivery
■
Laser Target & Rangefinder
■
Laser Spectroscopy
■
Avionics
■
Defense and Military
■
Life science
■
Airspace |
Features
■
Highest purity of silica fibers (UV,VIS,NIR)
■
Metal coated fibers (high temperature applications)
■
AR-coating of fiber end face
■
Air-Gap-Ferrule epoxy free
■
Custom design HP-SMA (High Power) connector -
(fiber tip incorporate a pure fused silica capillary)
■
Polished or Cleaved end face
■
ISO 9001:2008 certified production
■
Comprehensive quality control system |
Anatomy
of an Assembly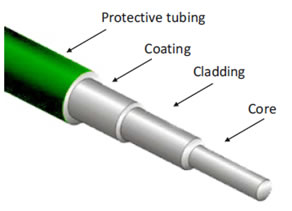
For
assembling Optical Cables the multimode fibers with core from pure fused
silica and the cladding from fluoride doped silica are used. A buffer
material is then applied. A buffer coats the core and cladding,
strengthens the fiber. In most assemblies polyimide is used as the
buffer; other assemblies use aluminum or acrylate. Then protective
tubing is applied over the core, cladding and buffer to protect the
fiber and provide strain relief. The standard jacketing is stainless
steel silicone monocoil. Precision optical Connectors terminate the
cable and are precisely aligned to ensure concentricity of the fiber.
Finally, end caps protect the fiber tips against scratches and
contaminants.
Choosing
the Right Fiber Cable for Laser Power Delivery
The most
critical issue in building Laser Power Delivery System is choosing the
right Optical Fiber Cable. Three main parameters are important to make
right selection:
1. Fiber
type & core diameter
2. Coating
and protective tube
3.
Connector
Choosing
the Fiber
One
important consideration in ordering an optical fiber assembly is which
fiber type you should specify for your application. Typically, the
wavelength range needed for your application should match the wavelength
range of the fiber type.
Low OH�
and High OH� Optical Fiber:
The optical attenuation characteristics are quite different for high OH�
and low OH� optical fiber core material. For UV-VIS spectral range (λ =
0,18 - 1,2 μm) Silica-Silica fibers with High OH� content should be used
and for VIS-NIR range (λ =0,35 -2,5 μm) � Silica-Silica fibers with Low
OH� group concentration are more convenient.
The next
significant parameter is the fiber core diameter. Smaller fiber cores
are preferred in order to get the best beam quality and high
flexibility. However optical fiber cables have several restrictions in
their power transmitting capabilities, and there are important
limitations to selecting the appropriate (smallest) fiber size. The
laser itself imposes constraints on the smallest fiber that can be used.
Maximum CW Power for Each Fiber Diameter |
|
Fiber Specifications |
Core dia.
(um) |
Square
(mm2) |
CW
power
(W) |
|
Core |
Pure silica |
50 |
0.0020 |
10 |
|
Cladding |
Fluorine doped fused silica |
100 |
0.0079 |
25 |
|
Coating |
Acrylate coating (-40 to 85oC) |
200 |
0.0314 |
50 |
|
Silicone resin coating (-40 to 180 oC) |
400 |
0.1256 |
100 |
|
Polyimide coating (-190 to 385 oC) |
600 |
0.2826 |
300 |
|
|
|
800 |
0.5024 |
600 |
|
|
|
1000 |
0.7850 |
800 |
|
|
|
Protective
tubing

Choosing
Connectors
Selecting
the right connector for your needs can be complicated by the many
choices available today. Choosing the best fiber optic connector for any
installation will have an impact on how efficient and cost-effective the
job is completed.
In today�s
Laser Power Fiber Delivery System, there are various optical fiber
connector types: SMA, ST, FC/PC, FC/APC, DL80, D-200 connectors,
cap-customized. Bespoken Mitsubishi connector design may include ferrule
protection by sapphire ring to prevent metal evaporation by intensive
laser beam.
High power
connectors feature an air-gap design, where the fiber extends into free
space b1.1mm to 1.5mm, providing an epoxy-free region where thermal
energy can be safely dissipated without burning the surrounding
material. This is the key mechanism for failure in standard connectors.
In addition
we utilize a number of unique methods of polishing fiber tip or fusing a
glass end cap to the end of the fiber (cap connector) to maximize power
handling.
High power
connectors compatible with SMA 905 and FC receptacles are offered.
Finally,
each cable assembly goes through the tight Quality Control with several
examinations during the fabrication process, including extensive
inspection of fiber tip quality by Fiber Check technique. Data will help
alleviate the confusion by reviewing the basic considerations prior to
deciding on the best connector for an installation.
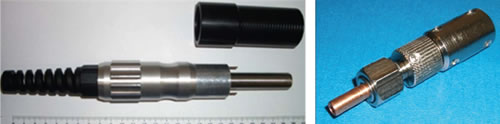
|
Laser-induced Damage in Fibers |
High
intensity of a laser beam can destroy a fiber. Theoretically it is
defined by damage threshold of a fiber. Unfortunately in practice fibers
and cables are often distracted because of improper handling. The most
general cause of such a destruction is an absorption of laser beam
energy by some object connected with the fiber. It can be, for example,
dust particles, which set on an endface of a fiber from air, or
particles of smoke' from the object, burned by the laser beam. So each
endface of a fiber must be watched before work and cleaned, if there are
some alien particles or stains on it. The output endface must be flowed
by clean air, if there is a possibility to stain it. When not used the
endface must be protected by a cover.
Input
connector may be heated because of improper coupling. The diameter of a
laser beam, focused by a coupling objective must be less than the
diameter of a fiber core. If there are wings in energy distribution,
because of high order modes or aberrations of the objective, they must
be cut off by a diaphragm. Aperture of a focused beam must be less than
aperture of a fiber also.
Laser beam,
formed by coupling objective, must be carefully micropositioned. Linear
displacement of input beam leads to heating of construction details and
also to destruction of a fiber.
Another
cause of fiber damage is a local energy concentration in fiber material.
It may occur if one puts an endface of a fiber before the waist of a
focused laser beam.
Proper
position of the endface is behind the waist (Fig.1). Angle displacement
of a beam leads to its focusing by a reflecting fiber core boundary and
to local energy concentration that destroys a fiber.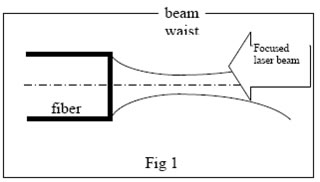
Micropositioning, of the input beam must be started from low level of
laser beam energy and be carried out very carefully. Sometimes the
damage occurs in the place of a hidden defect (alien particle, excessive
bending, or some other defect of structure).
In the case
of continuous radiation of CO2, laser and PIR-fiber, in spite of nearly
the same surface absorption for both ends, melting -starts from the
output end as a rule. It is caused by a superposition of direct and
reflected speckle patterns of light waves near the output end. Random
addition of these patterns leads to some local maximums, and melting
begins at the points with the highest local intensity. For IR fibers the
threshold intensity averaged over the whole cross-section is about 7-10
kW/cm2. This intensity can be increased by cooling of the end surface by
a flow of dry gas.
Investigations on the transmission of pulsed radiation of TEA CO2 laser
through polycrystalline fibers have shown that the damage usually occurs
in the initial part of a fiber at distances from several millimeters up
to several centimeters from the input end. Fiber damage threshold
induced by a pulse is significantly lower than in initial crystals. This
effect can be associated with the focusing of input radiation by the
cylindrical side the surface of the fiber. Estimated values of the
threshold in fibers with regard to the additional focusing correspond to
the bulk threshold at initial crystals.
Do not
hesitate to connect with us for technical consultation!
|
Fiber Delivery Fiber Optic Collimator
Optical Beam Delivery
Fiber
Coupled Diode Lasers Diode Driver |
|
|
|
|